મેટલ સ્ટ્રક્ચરલ મટિરિયલ્સમાં ટાઇટેનિયમ એલોય ઉત્પાદનોની વિશિષ્ટ તાકાત ખૂબ વધારે છે. તેની શક્તિ સ્ટીલની સમાન છે, પરંતુ તેનું વજન ફક્ત 57% સ્ટીલ છે. આ ઉપરાંત, ટાઇટેનિયમ એલોયમાં નાના વિશિષ્ટ ગુરુત્વાકર્ષણ, ઉચ્ચ થર્મલ તાકાત, સારી થર્મલ સ્થિરતા અને કાટ પ્રતિકારની લાક્ષણિકતાઓ છે, પરંતુ ટાઇટેનિયમ એલોય સામગ્રીને કાપવા અને ઓછી પ્રક્રિયા કાર્યક્ષમતા કરવી મુશ્કેલ છે. તેથી, ટાઇટેનિયમ એલોય પ્રોસેસિંગની મુશ્કેલી અને ઓછી કાર્યક્ષમતાને કેવી રીતે દૂર કરવી તે હંમેશાં તાકીદે હલ કરવામાં સમસ્યા રહી છે.
મુશ્કેલ ટાઇટેનિયમ એલોય પ્રોસેસિંગના કારણો
ટાઇટેનિયમ એલોયની થર્મલ વાહકતા ઓછી છે, તેથી ટાઇટેનિયમ એલોયની પ્રક્રિયા કરતી વખતે કટીંગ તાપમાન ખૂબ વધારે છે. સમાન પરિસ્થિતિઓમાં, પ્રોસેસિંગ ટીસી 4 [I] નું કટીંગ તાપમાન નંબર 45 સ્ટીલ કરતા બમણા વધારે છે. પ્રક્રિયા દરમિયાન ઉત્પન્ન થતી ગરમી વર્કપીસમાંથી પસાર થવી મુશ્કેલ છે. પ્રકાશન; ટાઇટેનિયમ એલોયની વિશિષ્ટ ગરમી ઓછી છે, અને પ્રક્રિયા દરમિયાન સ્થાનિક તાપમાન ઝડપથી વધે છે. તેથી, સાધનનું તાપમાન ખૂબ વધારે છે, ટૂલની ટોચ તીવ્ર પહેરે છે, અને સેવા જીવન ઓછું થાય છે.
ટાઇટેનિયમ એલોયની સ્થિતિસ્થાપકતાના નીચા મોડ્યુલસ [ii] મશિન સપાટીને પાછળના ભાગમાં સરળ બનાવે છે, ખાસ કરીને પાતળા-દિવાલોવાળા ભાગોની પ્રક્રિયાની પ્રક્રિયા વધુ ગંભીર છે, તે ફ્લ k ન્ક ચહેરા અને મશિન સપાટી વચ્ચે મજબૂત ઘર્ષણનું કારણ બનાવવાનું સરળ છે, જે સાધન પહેરે છે અને પતન કરશે. બ્લેડ.
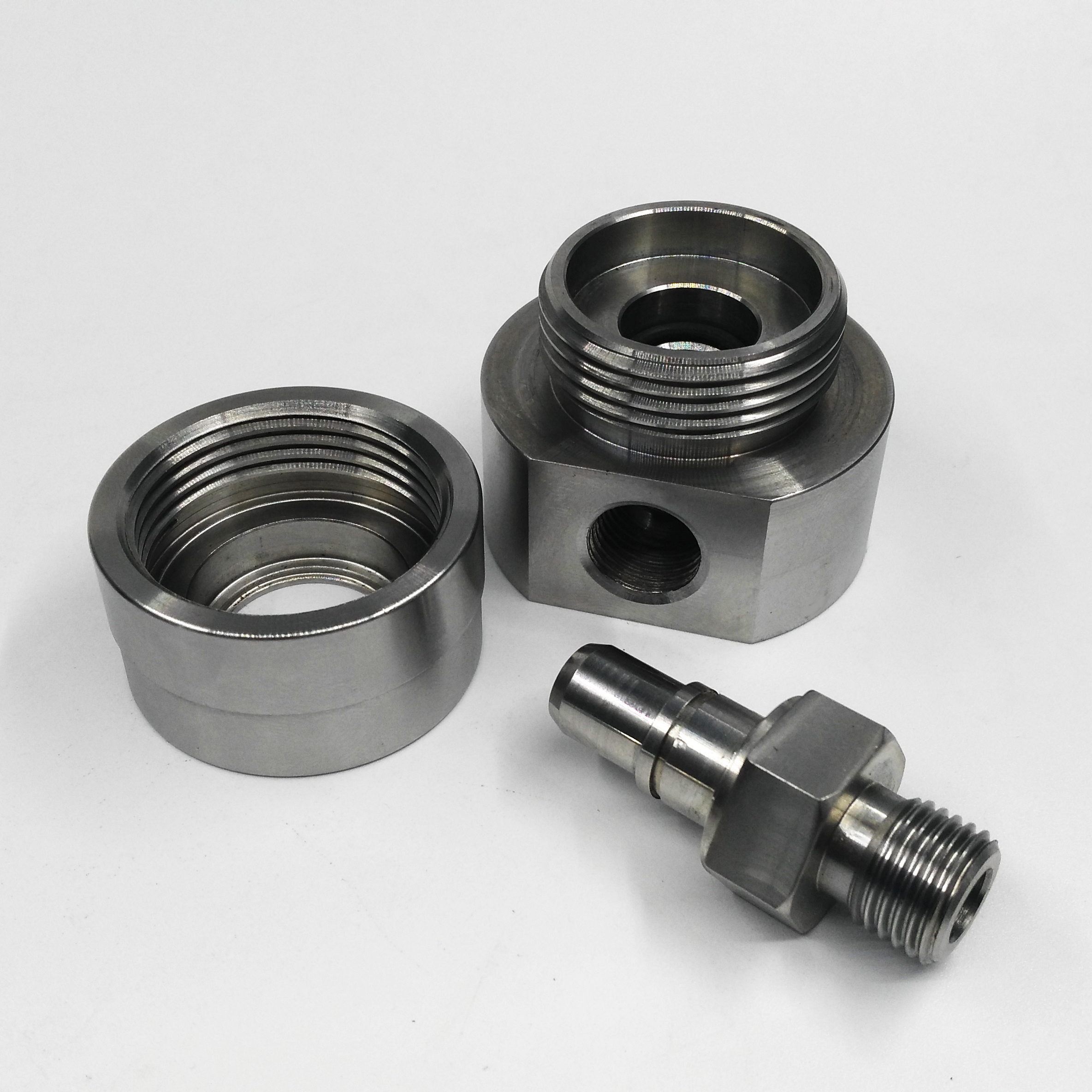
ટાઇટેનિયમ એલોય ખૂબ જ રાસાયણિક રીતે સક્રિય હોય છે અને temperatures ંચા તાપમાને ઓક્સિજન, હાઇડ્રોજન અને નાઇટ્રોજન સાથે સરળતાથી સંપર્ક કરે છે, તેમની શક્તિમાં વધારો કરે છે અને પ્લાસ્ટિસિટીમાં ઘટાડો થાય છે. હીટિંગ અને ફોર્જિંગ દરમિયાન રચાયેલ ઓક્સિજનથી સમૃદ્ધ સ્તર મશીનિંગને મુશ્કેલ બનાવે છે.
ટાઇટેનિયમ એલોય મટિરીયલ્સની પ્રક્રિયા કાપવાના સિદ્ધાંતો [1-3- 3-3]
મશીનિંગ પ્રક્રિયામાં, પસંદ કરેલી ટૂલ મટિરિયલ, કટીંગ શરતો અને કાપવાનો સમય બધા ટાઇટેનિયમ એલોય કટીંગની કાર્યક્ષમતા અને અર્થશાસ્ત્રને અસર કરશે.
1. વાજબી ટૂલ મટિરિયલ્સ પસંદ કરો
ટિટેનિયમ એલોય સામગ્રીની ગુણધર્મો, પ્રક્રિયા પદ્ધતિઓ અને પ્રક્રિયા તકનીકી પરિસ્થિતિઓને ધ્યાનમાં રાખીને, ટૂલ મટિરિયલ્સને વ્યાજબી રીતે પસંદ કરવી જોઈએ. ટૂલ મટિરિયલનો વધુ સામાન્ય રીતે ઉપયોગ કરવો જોઈએ, નીચા ભાવ, સારા વસ્ત્રો પ્રતિકાર, ઉચ્ચ થર્મલ કઠિનતા અને પૂરતી કઠિનતા હોવી જોઈએ.
2. કાપવાની સ્થિતિમાં સુધારો
મશીન ટૂલ-ફિક્સ્ચર-ટૂલ સિસ્ટમની કઠોરતા વધુ સારી છે. મશીન ટૂલના દરેક ભાગની મંજૂરી સારી રીતે ગોઠવવી જોઈએ, અને સ્પિન્ડલનો રેડિયલ રનઆઉટ નાનો હોવો જોઈએ. ફિક્સ્ચરનું ક્લેમ્પીંગ કાર્ય દ્ર firm અને સખત હોવું જોઈએ. સાધનનો કાપવાનો ભાગ શક્ય તેટલું ટૂંકા હોવું જોઈએ, અને જ્યારે ટૂલની શક્તિ અને કઠોરતા સુધારવા માટે ચિપ ક્ષમતા પૂરતી હોય ત્યારે કટીંગ ધારની જાડાઈ શક્ય તેટલી વધવી જોઈએ.
3. પ્રોસેસ્ડ સામગ્રી પર યોગ્ય ગરમીની સારવાર હાથ ધરવા
સામગ્રીની મશિનેબિલિટીમાં સુધારો લાવવાના હેતુને પ્રાપ્ત કરવા માટે, ટાઇટેનિયમ એલોય મટિરિયલ્સ [iii] ની ગુણધર્મો અને મેટલોગ્રાફિક રચનાને બદલવા માટે ગરમીની સારવાર દ્વારા.
4. વાજબી કાપવાની રકમ પસંદ કરો
કાપવાની ગતિ ઓછી હોવી જોઈએ. કારણ કે કટીંગની ગતિ કટીંગ ધારના તાપમાન પર મોટો પ્રભાવ ધરાવે છે, કટીંગની ગતિ વધારે છે, કટીંગ ધારના તાપમાનમાં તીવ્ર વધારો અને કટીંગ ધારનું તાપમાન સીધા ટૂલના જીવનને અસર કરે છે, તેથી પસંદ કરો. યોગ્ય કાપવાની ગતિ.
મશીનિંગ પ્રૌદ્યોગિકી
1. વળાંક
ટાઇટેનિયમ એલોય ઉત્પાદનોને સરળતાથી સપાટીની વધુ રફનેસ મેળવી શકે છે, અને કામ સખ્તાઇ ગંભીર નથી, પરંતુ કટીંગ તાપમાન વધારે છે અને ટૂલ ઝડપથી પહેરે છે. આ લાક્ષણિકતાઓને ધ્યાનમાં રાખીને, નીચેના પગલાં મુખ્યત્વે સાધનો અને કાપવાના પરિમાણોની દ્રષ્ટિએ લેવામાં આવે છે:
ટૂલ મટિરિયલ: વાયજી 6, વાયજી 8, વાયજી 10 એચટી ફેક્ટરીની હાલની પરિસ્થિતિઓ અનુસાર પસંદ કરવામાં આવે છે.
ટૂલ ભૂમિતિ પરિમાણો: ટૂલના યોગ્ય ફ્રન્ટ અને રીઅર એંગલ્સ, ટૂલ ટીપ રાઉન્ડિંગ.
ઓછી કટીંગ સ્પીડ, મધ્યમ ફીડ રેટ, deep ંડા કટીંગ depth ંડાઈ, પૂરતી ઠંડક, ટૂલ ટીપ બાહ્ય વર્તુળને ફેરવતી વખતે વર્કપીસના કેન્દ્ર કરતા વધારે ન હોઈ શકે, નહીં તો ટૂલને વીંધવું સરળ છે, અને સમાપ્ત કરતી વખતે ટૂલ પક્ષપાતી રહેશે વળાંક અને પાતળા-દિવાલોવાળા ભાગો ફેરવવું. કોણ મોટો હોવો જોઈએ, સામાન્ય રીતે 75-90 ડિગ્રી.
2. મિલિંગ
ટાઇટેનિયમ એલોય ઉત્પાદનોની મિલિંગ ફેરવવા કરતાં વધુ મુશ્કેલ છે, કારણ કે મિલિંગ તૂટક તૂટક કટીંગ છે, અને ચિપ્સ કટીંગ એજ સાથે બંધન કરવું સરળ છે. જ્યારે સ્ટીકી દાંત ફરીથી વર્કપીસમાં કાપી નાખે છે, ત્યારે સ્ટીકી ચિપ્સને પછાડી દેવામાં આવે છે અને ટૂલ મટિરિયલનો એક નાનો ટુકડો છીનવી લેવામાં આવે છે. ચિપિંગ ટૂલની ટકાઉપણું ઘટાડે છે.
મિલિંગ પદ્ધતિ: ક્લાઇમ્બીંગ મિલિંગનો ઉપયોગ સામાન્ય રીતે થાય છે.
ટૂલ મટિરિયલ: હાઇ સ્પીડ સ્ટીલ એમ 42.
સામાન્ય રીતે, એલોય સ્ટીલ [IV] ની મશીનિંગ ડાઉન મિલિંગનો ઉપયોગ કરતું નથી. મશીન ટૂલના સ્ક્રુ અને અખરોટ વચ્ચેના અંતરના પ્રભાવને કારણે, ડાઉન મિલિંગ દરમિયાન, મિલિંગ કટર વર્કપીસ પર કાર્ય કરે છે, અને ફીડ દિશામાં ઘટક બળ ફીડ દિશા જેવી જ છે. વર્કપીસ ટેબલની તૂટક તૂટક ચળવળ, પરિણામે છરી ફટકો પડ્યો. ડાઉન મિલિંગ માટે, કટર દાંત કટની શરૂઆતમાં પોપડાને ફટકારે છે, જેના કારણે કટર તૂટી જાય છે. તેમ છતાં, કારણ કે અપ-મિલિંગ ચિપ્સ પાતળાથી જાડા સુધી બદલાય છે, ટૂલ પ્રારંભિક કટીંગ દરમિયાન વર્કપીસ સાથે સુકા ઘર્ષણ કરવાનું જોખમ ધરાવે છે, જે ટૂલને ચોંટતા અને ચિપિંગમાં વધારો કરે છે. ટાઇટેનિયમ એલોયને સરળતાથી મિલિંગ બનાવવા માટે, તે પણ નોંધવું જોઇએ કે રેક એંગલ ઘટાડવો જોઈએ અને સામાન્ય સ્ટાન્ડર્ડ મિલિંગ કટરની તુલનામાં રાહત એંગલ વધારવો જોઈએ. મિલિંગની ગતિ ઓછી હોવી જોઈએ, અને રાહત ટૂથ મિલિંગ કટરના ઉપયોગને ટાળવા માટે દાંતના મીલિંગ કટરનો ઉપયોગ શક્ય તેટલો કરવો જોઈએ.
3. ટેપીંગ
ટાઇટેનિયમ એલોય ઉત્પાદનોના ટેપીંગ માટે, નાના ચિપ્સને કારણે, બ્લેડ અને વર્કપીસ સાથે બંધન કરવું સરળ છે, પરિણામે મોટી સપાટીની રફનેસ અને વિશાળ ટોર્ક. ટેપ કરતી વખતે, અયોગ્ય પસંદગી અને નળનું અયોગ્ય કામગીરી [વી] સરળતાથી કામ સખ્તાઇનું કારણ બની શકે છે, પ્રક્રિયા કાર્યક્ષમતા ખૂબ ઓછી હોય છે, અને કેટલીકવાર નળ તૂટી જાય છે.
પ્રથમ સ્થાને વાયર સાથે જમ્પ-ટૂથ ટેપનો ઉપયોગ કરવો જરૂરી છે, અને દાંતની સંખ્યા પ્રમાણભૂત નળ કરતા ઓછી હોવી જોઈએ, સામાન્ય રીતે 2 થી 3 દાંત. કટીંગ ટેપર એંગલ મોટો હોવો જોઈએ, અને ટેપર ભાગ સામાન્ય રીતે 3 થી 4 થ્રેડ લંબાઈનો હોય છે. ચિપ દૂર કરવાની સુવિધા માટે, નકારાત્મક ઝોક એંગલ પણ કાપવાના શંકુ પર જમીન હોઈ શકે છે. નળની કઠોરતા વધારવા માટે ટૂંકા નળ પસંદ કરવાનો પ્રયાસ કરો. નળનો ver ંધી ટેપર ભાગ નળ અને વર્કપીસ વચ્ચેના ઘર્ષણને ઘટાડવા માટે ધોરણની તુલનામાં યોગ્ય રીતે વિસ્તૃત થવો જોઈએ.
4. રીમિંગ
હેન ટાઇટેનિયમ એલોય રીમિંગ, ટૂલ વસ્ત્રો ગંભીર નથી, અને સિમેન્ટ કાર્બાઇડ અને હાઇ સ્પીડ સ્ટીલ રીમરનો ઉપયોગ કરી શકાય છે. સિમેન્ટ કાર્બાઇડ રીમરનો ઉપયોગ કરતી વખતે, રીમેરને ચિપિંગથી બચાવવા માટે ડ્રિલિંગની સમાન પ્રક્રિયા સિસ્ટમની કઠોરતા અપનાવવી જોઈએ. ટાઇટેનિયમ એલોય રીમિંગની મુખ્ય સમસ્યા એ રીમિંગની નબળી પૂર્ણાહુતિ છે. બ્લેડને છિદ્રની દિવાલને વળગી રહેતા અટકાવવા માટે, રીમર બ્લેડની પહોળાઈને સંકુચિત કરવા માટે વ્હીટ્સનનો ઉપયોગ કરવો આવશ્યક છે, પરંતુ પૂરતી તાકાત સુનિશ્ચિત કરવી આવશ્યક છે. સામાન્ય રીતે, બ્લેડની પહોળાઈ 0.1 ~ 0.15 મીમી પણ હોય છે.
કટીંગ ધાર અને કેલિબ્રેશન ભાગ વચ્ચેનું સંક્રમણ સરળ ચાપ હોવું જોઈએ, અને તે વસ્ત્રો પછી સમયસર તીક્ષ્ણ થવું જોઈએ, અને દરેક દાંતની ચાપનું કદ સમાન હોવું જોઈએ; જો જરૂરી હોય તો, કેલિબ્રેશન ભાગની ver ંધી શંકુ વિસ્તૃત કરી શકાય છે.
5. ડ્રિલિંગ
ટાઇટેનિયમ એલોયને ડ્રિલ કરવું મુશ્કેલ છે, અને બર્નિંગ ટૂલ્સ અને તૂટેલી કવાયતની ઘટના ઘણીવાર પ્રક્રિયા દરમિયાન થાય છે. આ મુખ્યત્વે ઘણા કારણોસર થાય છે જેમ કે ડ્રિલ બીટની નબળી શાર્પિંગ, વિલંબિત ચિપ દૂર કરવા, નબળી ઠંડક અને પ્રક્રિયા સિસ્ટમની નબળી કઠોરતા. તેથી, ટાઇટેનિયમ એલોય ડ્રિલિંગ પ્રક્રિયામાં વાજબી કવાયત શાર્પિંગ પર ધ્યાન આપવું જરૂરી છે, શિરોબિંદુ કોણ વધારવું, બાહ્ય ધારનો આગળનો ખૂણો ઘટાડવું, બાહ્ય ધારનો પાછળનો ખૂણો વધારવો, અને ver ંધી ટેપરને 2 થી વધારીને વધારી દેવું પ્રમાણભૂત કવાયત કરતા 3 ગણા. છરી વારંવાર પાછી ખેંચો અને ચિપ્સના આકાર અને રંગ પર ધ્યાન આપીને, સમયસર ચિપ્સને દૂર કરો. જો ડ્રિલિંગ પ્રક્રિયા દરમિયાન ચિપ્સ પીંછા અથવા રંગ બદલાય છે, તો તે સૂચવે છે કે કવાયત અસ્પષ્ટ છે, અને સમયને ટૂલ બદલવા અને તીક્ષ્ણ બનાવવી જોઈએ.
ડ્રિલિંગ જિગને વર્કટેબલ પર ઠીક કરવી જોઈએ. ડ્રિલિંગ જિગનો માર્ગદર્શક ચહેરો પ્રોસેસિંગ સપાટીની નજીક હોવો જોઈએ, અને ટૂંકા કવાયત બીટનો ઉપયોગ શક્ય તેટલું કરવો જોઈએ. બીજી નોંધપાત્ર સમસ્યા એ છે કે જ્યારે મેન્યુઅલ ફીડ અપનાવવામાં આવે છે, ત્યારે કવાયતને છિદ્રમાં આગળ વધવા અથવા પીછેહઠ કરવી જોઈએ નહીં, નહીં તો કવાયત બ્લેડ મશિન સપાટી સામે ઘસશે, જેનાથી કામ સખ્તાઇ અને કવાયતને ઓછી થાય છે.
6. ગ્રાઇન્ડીંગ
ગ્રાઇન્ડીંગ ટાઇટેનિયમ એલોય ભાગોમાં સામાન્ય સમસ્યાઓ સ્ટીકી કાટમાળ છે જે ગ્રાઇન્ડીંગ વ્હીલના અવરોધનું કારણ બને છે અને ભાગની સપાટી પર બળી જાય છે. કારણ એ છે કે ટાઇટેનિયમ એલોયની નબળી થર્મલ વાહકતા, જે ગ્રાઇન્ડીંગ ઝોનમાં temperature ંચા તાપમાનનું કારણ બને છે, જેથી ટાઇટેનિયમ એલોય અને ઘર્ષક બંધાયેલા, વિખરાયેલા અને રાસાયણિક રીતે પ્રતિક્રિયા આપવામાં આવે. સ્ટીકી ચિપ્સ અને ગ્રાઇન્ડીંગ વ્હીલનું અવરોધ ગ્રાઇન્ડીંગ રેશિયોમાં નોંધપાત્ર ઘટાડો તરફ દોરી જાય છે. ફેલાવો અને રાસાયણિક પ્રતિક્રિયાઓના પરિણામે, વર્કપીસ જમીનની સપાટી પર સળગાવી દેવામાં આવે છે, પરિણામે ભાગોની થાક શક્તિમાં ઘટાડો થાય છે, જે ટાઇટેનિયમ એલોય કાસ્ટિંગ્સને ગ્રાઇન્ડીંગ કરતી વખતે વધુ સ્પષ્ટ છે.
આ સમસ્યાને હલ કરવા માટે, લેવામાં આવેલા પગલાં આ છે:
યોગ્ય ગ્રાઇન્ડીંગ વ્હીલ સામગ્રી પસંદ કરો: ગ્રીન સિલિકોન કાર્બાઇડ ટી.એલ. સહેજ નીચી ગ્રાઇન્ડીંગ વ્હીલ સખ્તાઇ: ઝેડઆર 1.
ટાઇટેનિયમ એલોય મટિરીયલ પ્રોસેસિંગની એકંદર કાર્યક્ષમતામાં સુધારો કરવા માટે ટ્યુલ મટિરિયલ્સ, કટીંગ ફ્લુઇડ્સ અને મશીનિંગ પ્રક્રિયા પરિમાણોની દ્રષ્ટિએ ટાઇટેનિયમ એલોય સામગ્રીના કાપને નિયંત્રિત કરવું આવશ્યક છે.