ઉપરોક્ત કારણો ઉપરાંત, પ્રક્રિયા દરમિયાન એલ્યુમિનિયમ ભાગો વિકૃત કરે છે. વાસ્તવિક કામગીરીમાં, ઓપરેશન પદ્ધતિ પણ ખૂબ જ મહત્વપૂર્ણ છે.
મોટા મશીનિંગ ભથ્થાઓવાળા ભાગો માટે, મશીનિંગ પ્રક્રિયા દરમિયાન ગરમીની વધુ સારી પરિસ્થિતિઓ અને ગરમીની સાંદ્રતાને ટાળવા માટે, મશીનિંગ દરમિયાન સપ્રમાણ મશીનિંગનો ઉપયોગ કરવો જોઈએ. જો ત્યાં mm૦ મીમીની જાડા શીટ છે જેની પ્રક્રિયા 60 મીમી સુધી કરવાની જરૂર છે, જો એક બાજુ મિલ્ડ કરવામાં આવે છે અને બીજી બાજુ તરત જ મિલ્ડ કરવામાં આવે છે, અને અંતિમ કદ એકવાર પ્રક્રિયા કરવામાં આવે છે, તો ફ્લેટનેસ 5 મીમી સુધી પહોંચશે; જો પુનરાવર્તિત ફીડ સપ્રમાણ પ્રક્રિયાનો ઉપયોગ કરવામાં આવે છે, તો દરેક બાજુ બે વાર પ્રક્રિયા કરવામાં આવે છે અંતિમ કદ 0.3 મીમીની ચપળતાની બાંયધરી આપી શકે છે. જો પ્લેટના ભાગ પર બહુવિધ પોલાણ હોય, તો પ્રક્રિયા દરમિયાન પોલાણ-બાય-હોલીટી ક્રમિક પ્રોસેસિંગ પદ્ધતિનો ઉપયોગ કરવાની સલાહ આપવામાં આવતી નથી, કારણ કે આ સરળતાથી અસમાન દળો અને ભાગોના વિકૃતિનું કારણ બનશે. મલ્ટિ-લેયર પ્રોસેસિંગ અપનાવવામાં આવે છે, અને દરેક સ્તર શક્ય તેટલું શક્ય તેટલું જ સમયે બધી પોલાણ પર પ્રક્રિયા કરવામાં આવે છે, અને પછીના સ્તરની પ્રક્રિયા ભાગોને સમાનરૂપે તાણમાં બનાવવા અને વિરૂપતાને ઘટાડવા માટે કરવામાં આવે છે.
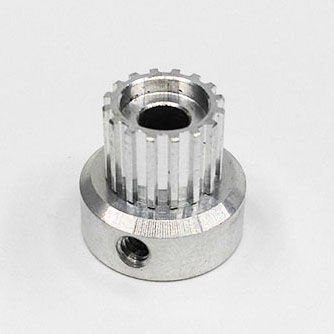
કટીંગની રકમ બદલીને કટીંગ ફોર્સ અને કટીંગ ગરમી ઘટાડે છે. કાપવાની રકમના ત્રણ તત્વોમાં, બેક-કટીંગની માત્રાને કાપવા બળ પર મોટો પ્રભાવ છે. જો મશીનિંગ ભથ્થું ખૂબ મોટું હોય, તો પાસનો કટીંગ બળ ખૂબ મોટો છે, જે ફક્ત ભાગોને વિકૃત કરશે નહીં, પણ મશીન ટૂલ સ્પિન્ડલની કઠોરતાને પણ અસર કરશે અને ટૂલની ટકાઉપણું ઘટાડે છે. જો તમે છરીઓની માત્રાને ઘટાડશો, તો ઉત્પાદન કાર્યક્ષમતામાં મોટા પ્રમાણમાં ઘટાડો થશે. જો કે, સીએનસી મશીનિંગમાં હાઇ સ્પીડ મિલિંગનો ઉપયોગ થાય છે, જે આ સમસ્યાને દૂર કરી શકે છે. બેક-ગ્ર rab બિંગની માત્રાને ઘટાડતી વખતે, જ્યાં સુધી ફીડ અનુરૂપ રીતે વધારવામાં આવે છે અને મશીન ટૂલની ગતિમાં વધારો થાય છે, ત્યાં સુધી પ્રક્રિયાની કાર્યક્ષમતાની ખાતરી કરતી વખતે કટીંગ બળ ઘટાડી શકાય છે.
છરીના હુકમ પર પણ ધ્યાન આપો. રફ મશીનિંગ મશીનિંગ કાર્યક્ષમતામાં સુધારણા અને એકમ સમય દીઠ દૂર કરવાના દરની શોધ પર ભાર મૂકે છે. સામાન્ય રીતે, અપ-કટ મિલિંગનો ઉપયોગ કરી શકાય છે. એટલે કે, કોરાની સપાટી પરની વધુ સામગ્રીને ઝડપી ગતિ અને ટૂંકા સમય પર દૂર કરવામાં આવે છે, અને સમાપ્ત કરવા માટે જરૂરી ભૌમિતિક સમોચ્ચ મૂળભૂત રીતે રચાય છે. સમાપ્ત થવાનો ભાર ઉચ્ચ ચોકસાઇ અને ઉચ્ચ ગુણવત્તા છે, અને ડાઉન મિલિંગનો ઉપયોગ થવો જોઈએ. કારણ કે કટર દાંતની કાપવાની જાડાઈ ધીમે ધીમે ડાઉન મિલિંગ દરમિયાન મહત્તમથી શૂન્ય સુધી ઘટે છે, કામ સખ્તાઇની ડિગ્રી ખૂબ ઓછી થાય છે, અને તે જ સમયે ભાગોના વિકૃતિની ડિગ્રી ઓછી થાય છે.
પ્રક્રિયા દરમિયાન ક્લેમ્પિંગને કારણે પાતળા-દિવાલોવાળી વર્કપીસ વિકૃત થાય છે, અને અંતિમ પણ અનિવાર્ય છે. વર્કપીસના વિરૂપતાને ઘટાડવા માટે, અંતિમ પ્રક્રિયાના અંતિમ કદ સુધી પહોંચે તે પહેલાં પ્રેસિંગ પીસ oo ીલું કરી શકાય છે, જેથી વર્કપીસને તેના મૂળ આકારમાં મુક્તપણે પુન restored સ્થાપિત કરી શકાય, અને પછી સહેજ સંકુચિત, કઠોર ક્લેમ્પિંગને આધિન, વર્કપીસ (સંપૂર્ણ રીતે હાથ દ્વારા), આદર્શ પ્રક્રિયા અસર આ રીતે મેળવી શકાય છે. ટૂંકમાં, ક્લેમ્પીંગ ફોર્સની ક્રિયાનો મુદ્દો સહાયક સપાટી પર શ્રેષ્ઠ છે, અને ક્લેમ્પીંગ ફોર્સે વર્કપીસની સારી કઠોરતાની દિશામાં કાર્ય કરવું જોઈએ. વર્કપીસ oo ીલું ન થાય તે સુનિશ્ચિત કરવાના આધાર હેઠળ, ક્લેમ્પીંગ ફોર્સ જેટલું નાનું છે.
જ્યારે પોલાણ સાથેના ભાગોને મશીન કરવામાં આવે છે, ત્યારે મિલિંગ કટરને કવાયત બીટની જેમ સીધા ભાગમાં ડૂબવાની મંજૂરી આપવાનો પ્રયાસ ન કરો, પરિણામે મિલિંગ કટર, અનસમૂથ ચિપ દૂર કરવા, અને ઓવરહિટીંગ, વિસ્તરણ અને ટૂલ પતન માટે અપૂરતી ચિપ જગ્યા. તૂટેલા છરી જેવી બિનતરફેણકારી ઘટના. પ્રથમ, મિલિંગ કટર અથવા એક કદ મોટા જેવા જ કદની કવાયતથી છિદ્રને કવાયત કરો, અને પછી તેને મિલિંગ કટરથી મિલ કરો. વૈકલ્પિક રીતે, સીએએમ સ software ફ્ટવેરનો ઉપયોગ સર્પાકાર કટીંગ પ્રોગ્રામના નિર્માણ માટે થઈ શકે છે.